GI pipe manufacturing and installation: check these safety factors
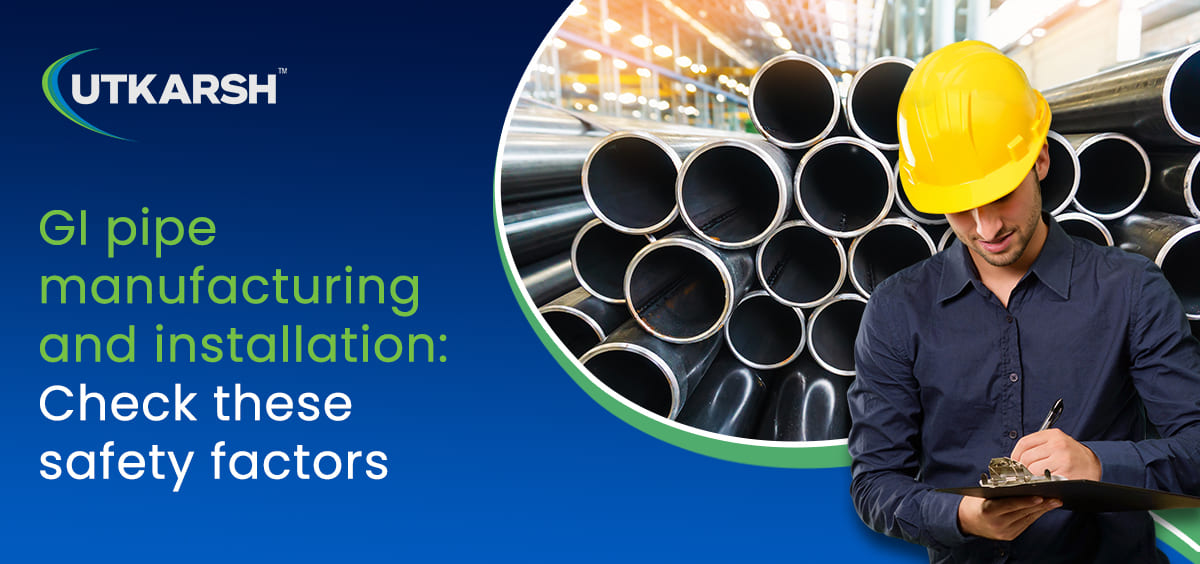
Galvanised Iron (GI) pipes are highly sought after in numerous industries due to their exceptional durability and corrosion-resistant attributes. These pipes exhibit remarkable resistance to rust and corrosion, making them suitable for applications where exposure to moisture or harsh environments is a concern. However, it is crucial to prioritise safety measures throughout both the manufacturing and installation processes to ensure the optimal performance and longevity of these pipes. As one of the leading GI pipe manufacturers, we share some of the insights into maintaining safety during the manufacturing and installation of GI pipes.
Adequate training and competency
By prioritising training and competency development, businesses can empower their employees with the knowledge and skills needed to carry out GI pipe manufacturing and installation safely and with high quality. To prioritise training and competency development in GI pipe manufacturing and installation, businesses should establish a comprehensive training program that covers all relevant aspects of the job. This program should encompass operating machinery, handling tools, and following safety protocols specific to the business and its employees. Hands-on training, conducted by experienced and qualified trainers, should be provided to ensure employees learn how to use machinery and tools safely.
Encouraging employees to ask questions and actively practise the skills they have learned is essential. This fosters confidence in their abilities and reinforces the correct application of safety protocols. Regular assessments of the training program should be conducted to ensure its effectiveness and to make necessary updates in line with changing workplace conditions or safety standards.
Proper handling of materials
Ensuring the safety of workers and preventing accidents is of utmost importance when handling GI pipe materials. To prioritise safe handling, businesses should adhere to the following guidelines:
● They should store GI pipes in designated areas that are free from walkways and other high-traffic zones. By doing so, businesses can minimise tripping hazards and reduce the risk of workers stumbling over pipes, thus preventing potential injuries.
● When dealing with heavy GI pipes, businesses should employ suitable lifting techniques and equipment like cranes or forklifts. This approach is essential as manually lifting heavy pipes can be hazardous and increase the likelihood of accidents. By using proper lifting equipment, businesses ensure the safe transportation of heavy pipes, protecting the well-being of workers.
● Businesses should establish guidelines for stacking and organising pipes to prevent collapse or shifting during storage or transportation. Properly stacked and organised pipes ensure stability and reduce the chances of accidents or injuries caused by collapsing or shifting pipes.
Maintenance and inspection of equipment
To maintain a safe and efficient operation, businesses should prioritise the regular inspection and maintenance of manufacturing and installation equipment. This includes creating a preventive maintenance schedule for machinery used in tasks such as pipe-cutting, welding, and threading. Conducting routine inspections is important to identify and address potential hazards that may arise from faulty electrical connections or worn-out components. Also, it is important to encourage workers to promptly report any equipment malfunctions or defects they observe.
Ventilation and respiratory protection
It is important to maintain proper ventilation systems at the manufacturing and welding sites to minimise exposure to harmful fumes and dust. Some of the safety guidelines that businesses should follow include:
● Install exhaust fans or use portable ventilation units to ensure fresh air circulation. This will help to remove harmful fumes and dust from the air and reduce the risk of exposure.
● Provide workers with appropriate respiratory protective equipment, such as masks or respirators, to reduce inhalation of hazardous particles or gases. This equipment should be properly fitted and worn at all times when workers are exposed to hazardous fumes or dust.
Fire safety and precaution
Are you looking for a reliable GI pipe manufacturer?
Explore our comprehensive range of GI and MS pipes. We aim to meet the diverse requirements of our customers across various industries, ensuring durability, reliability, and high-performance standards.
We take pride in manufacturing products that comply with industry standards and possess the necessary certifications. Our pipes adhere to prominent IS licences such as IS 1239, IS 3601, IS 1161, and IS 3589. This commitment to meeting established standards ensures that our products meet stringent quality requirements, delivering reliability and performance to our customers.
Our pipes offer a wide range of specifications to meet diverse requirements:
● Thickness: Our pipes have a thickness ranging from 1.80 mm to 9.50 mm, allowing for versatility and durability in various applications.
● Hollow Sections: We provide hollow sections with dimensions ranging from 19.5 mm x 19.5 mm to 220 mm x 220 mm, catering to different structural needs.
● Pipe Length: Our pipes are available in lengths ranging from 4 metres to 12 metres (DRL), offering flexibility for different project requirements.
● Surface Finish: Choose from a variety of surface finishes, including Black Painted, Self-coloured/Mill Varnished, and Galvanised options. Each finish provides specific benefits such as corrosion resistance or enhanced aesthetics.
● End Finish: We offer different end finishes to suit specific installation needs. Options include Plain Square Cut Ends, Screwed & Socketed Ends, and Grooved Ends with Victaulic Roll Grooving. This variety ensures compatibility with various piping systems and installation methods.